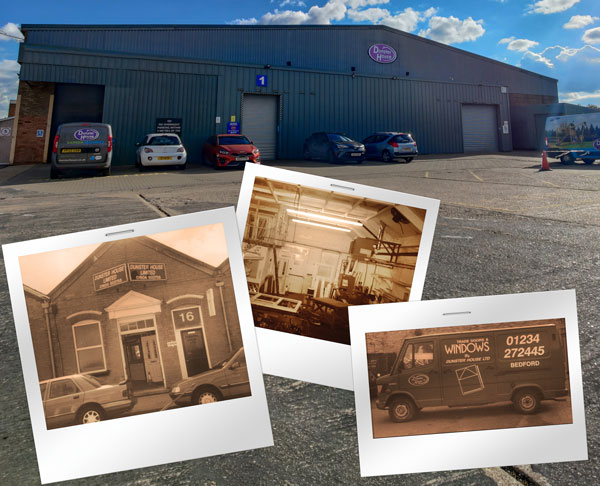
We are a family owned and run business
That has been designing and supplying business and leisure garden products for over three decades since its formation by Christopher Murphy MBE and Pamela Murphy in 1994. What started out as a humble company in a 1000sq/ft factory has developed into the business empire it is today.
Nowadays Chris and Pam’s sons, Alexander and Andrew, have long since joined them in helming our good ship, Dunster House, and the company goes from strength to strength, continuing to strive to meet our customers’ high expectations.
Dunster House are unique within the marketplace as all its design concepts are created in the UK before being manufactured in one of the 11 Factory Units in the UK and the 14 Factory Units in Europe. All of the prototyping and testing is conducted in the UK to make sure products withstand practical use.
Our greatest achievement is in employing staff, now over 860 throughout the UK and Europe with a view to recruit 120 additional staff by the end of 2025.
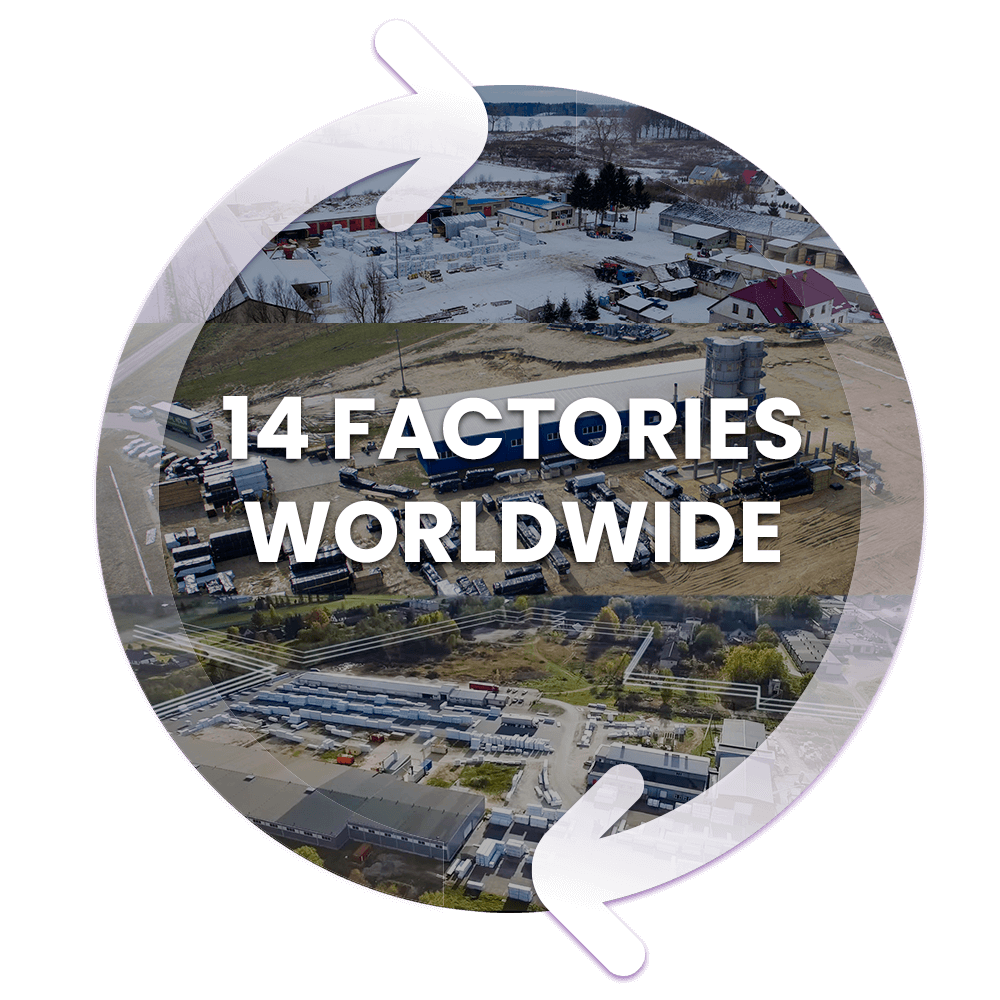
These factories are also owned by members of the same Murphy family and are spread across 8 giant sites in Europe. This enables complete control over every process, from purchasing the timber to final distribution to you. All our raw materials are sourced from sustainable sources and are of the highest quality.
These manufacturing factories use the latest technology to produce the best quality items, at an affordable price, with a highly trained work force.
Numerous UK Distribution Depots
All our business is via our company website or by phone.
Across the UK, we currently have 14 distribution centres, helping us get our products delivered to you as efficiently as possible. With the ability to demonstrate that we never compromise on quality, our attention to detail and affordability, our highly trained staff are courteous, knowledgeable and happy to discuss your requirements, from initial contact to aftercare. Dunster House are a customer-focused and driven company and has built a reputation for its high standards and competitive prices. Our goal is 100% customer satisfaction!
Please note that we do not have physical show sites where our products can be viewed.
- Bedford HQ
- Bedford Factory
- Warminster Branch
- Faversham Branch
- Basingstoke Branch
- Liverpool Branch
- Flixborough Branch
- Witham Branch
- Gosberton Factory
- Huntly Factory
- Cumbernauld Factory
- Dudley Branch
- Spalding Branch
- Stockton on Tees Branch
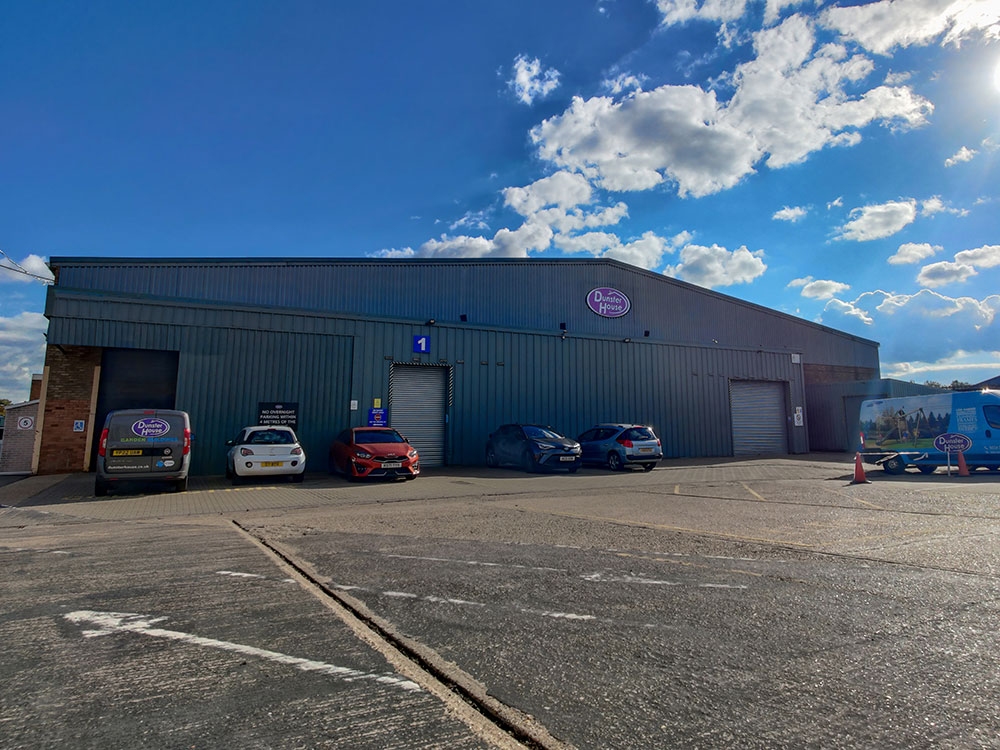
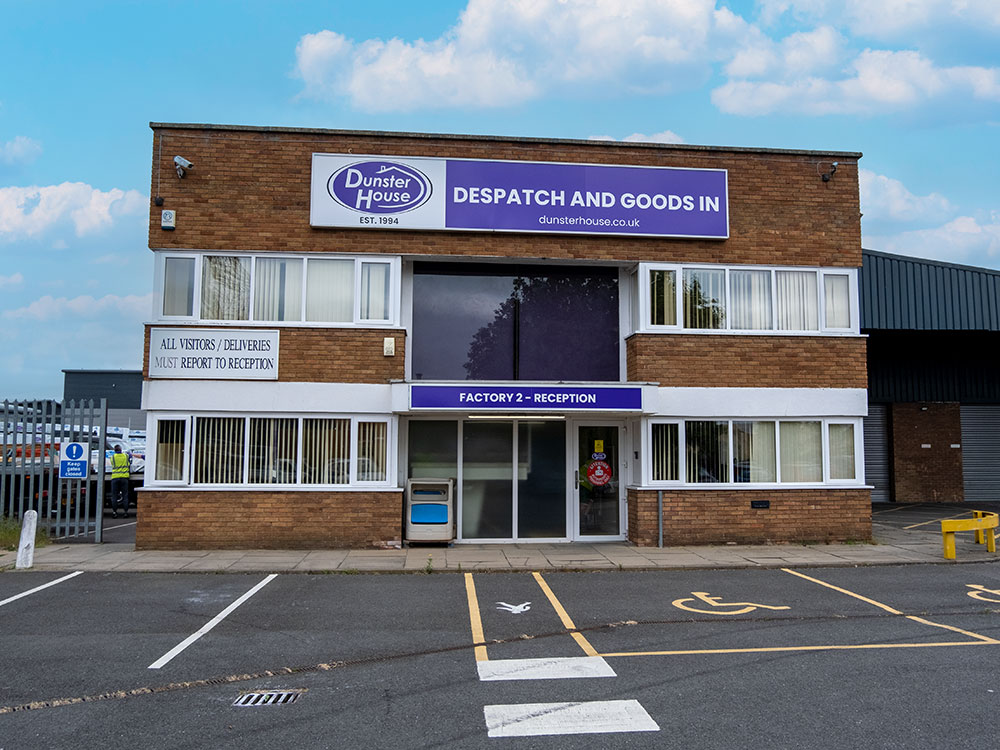
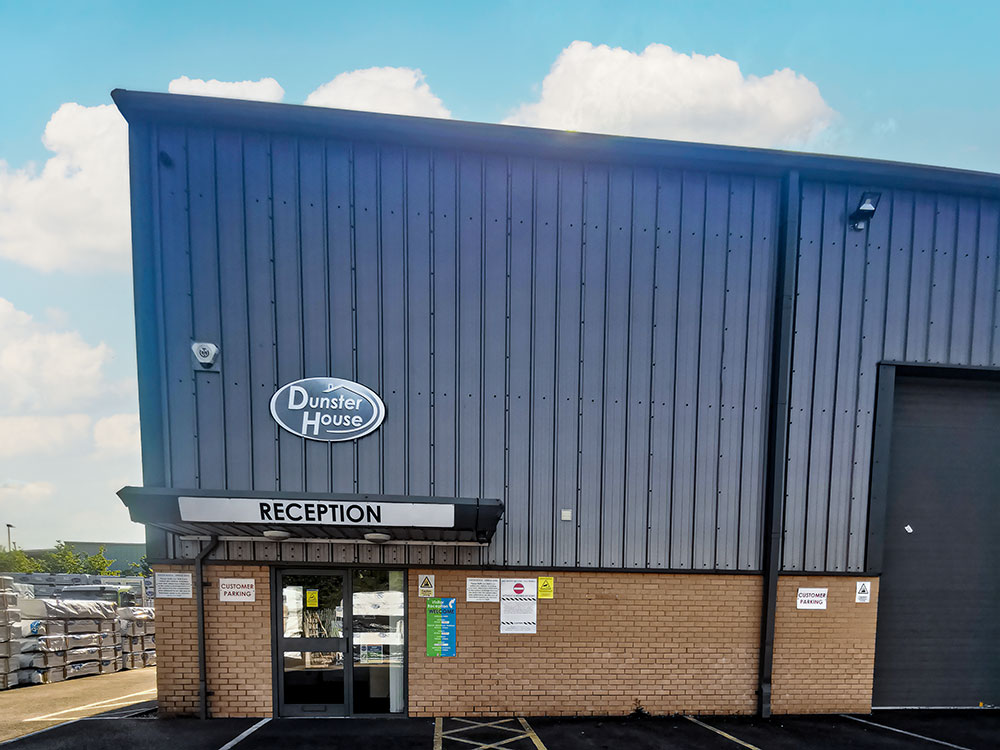
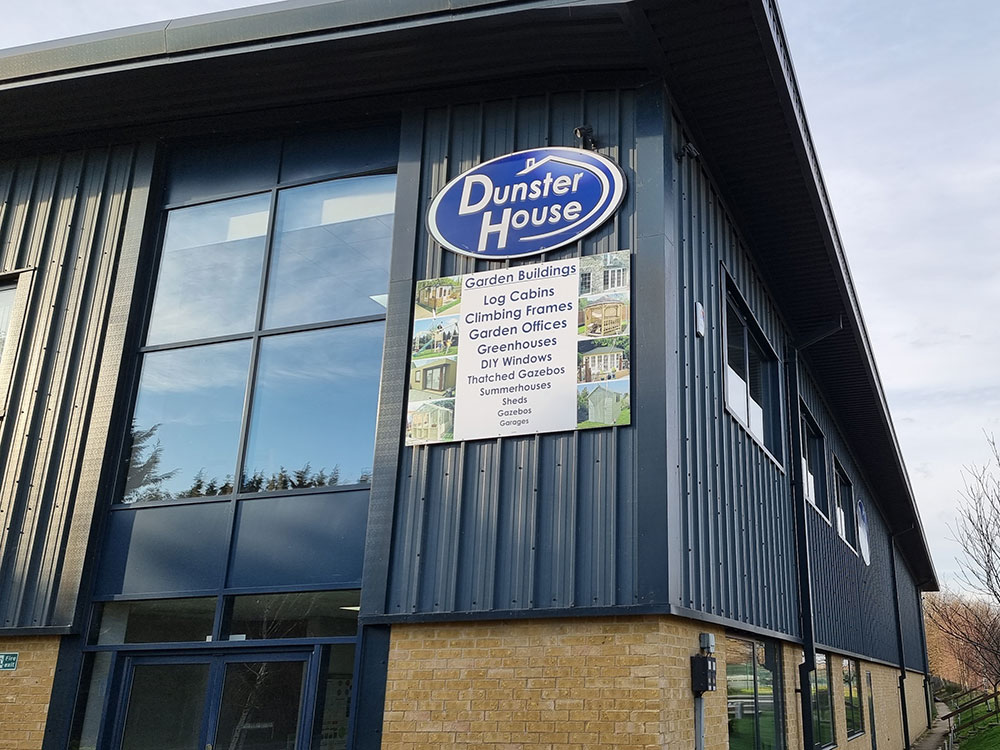
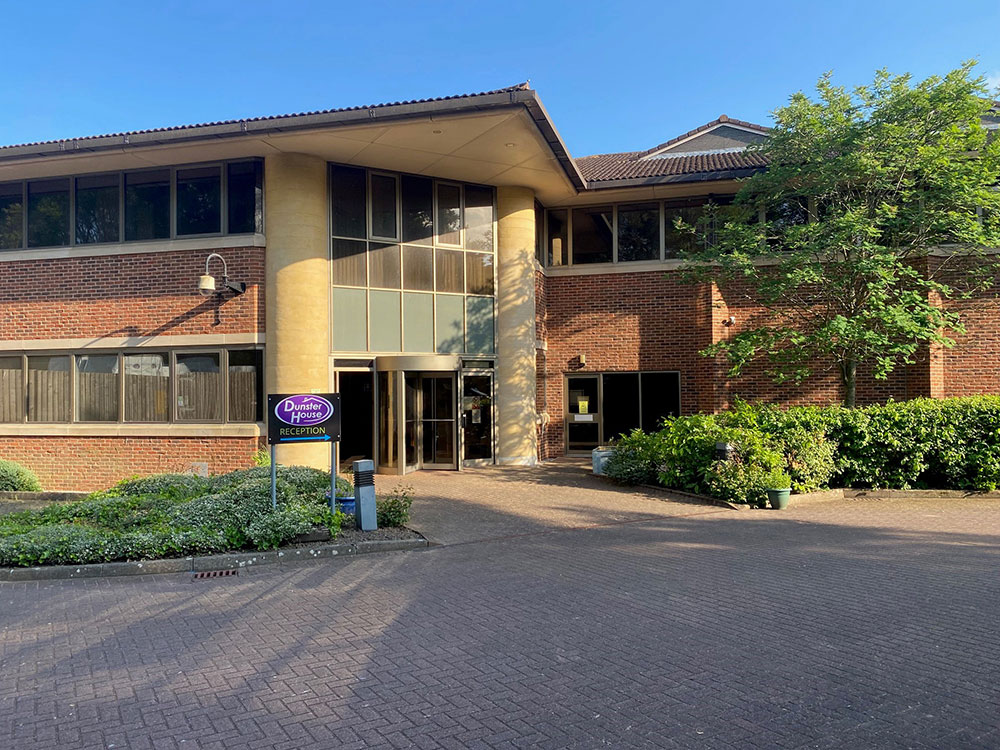
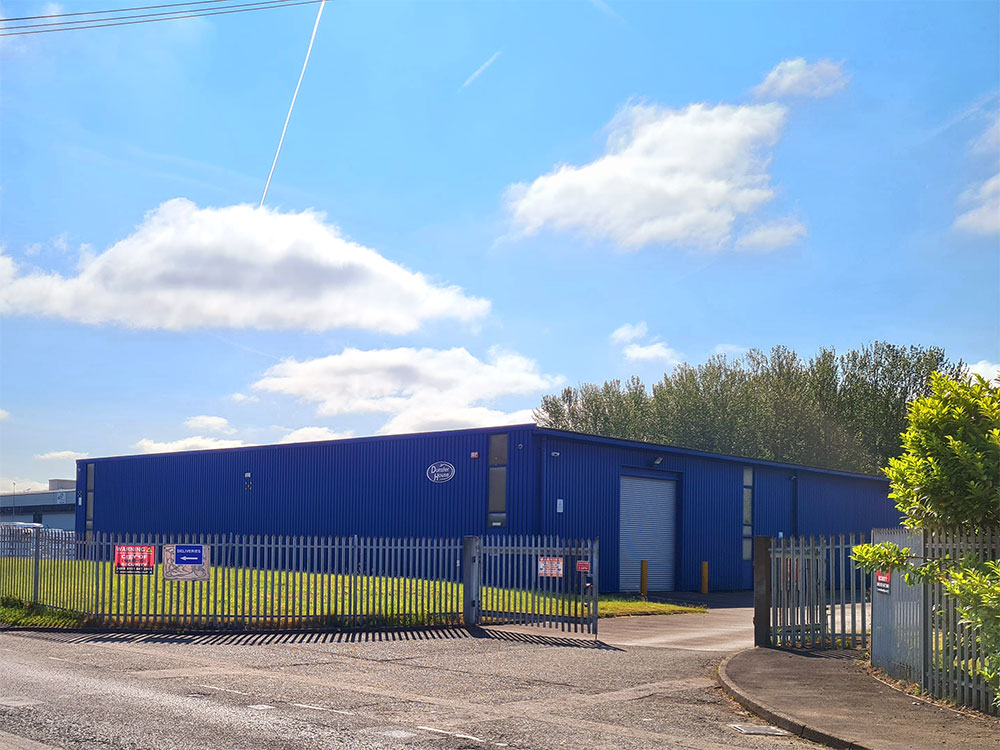
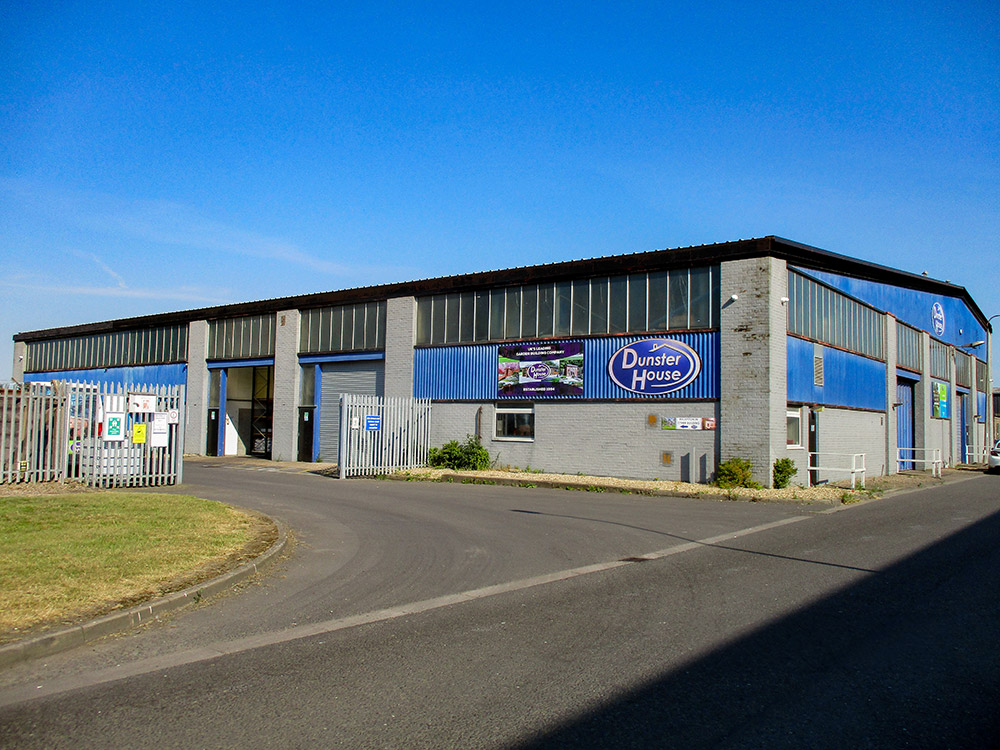
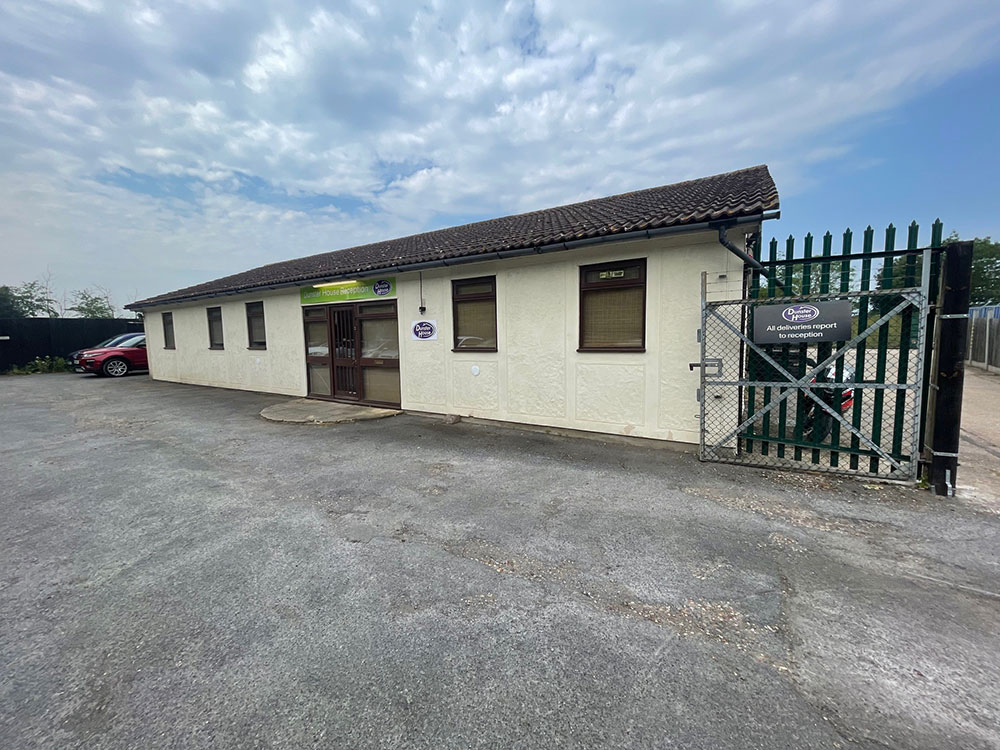
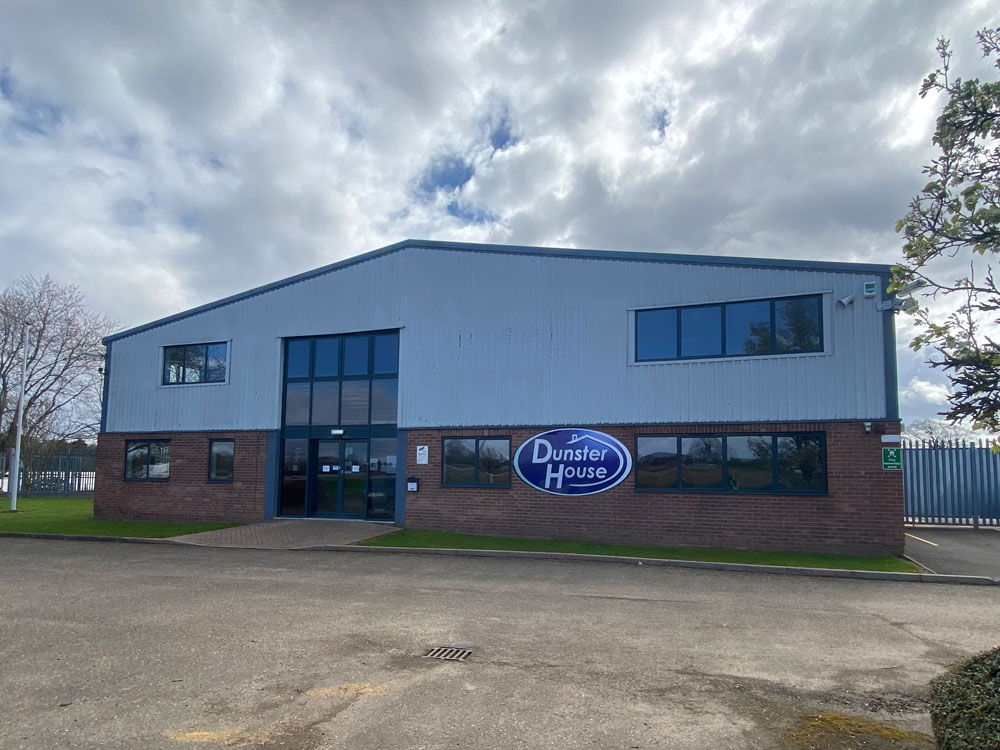
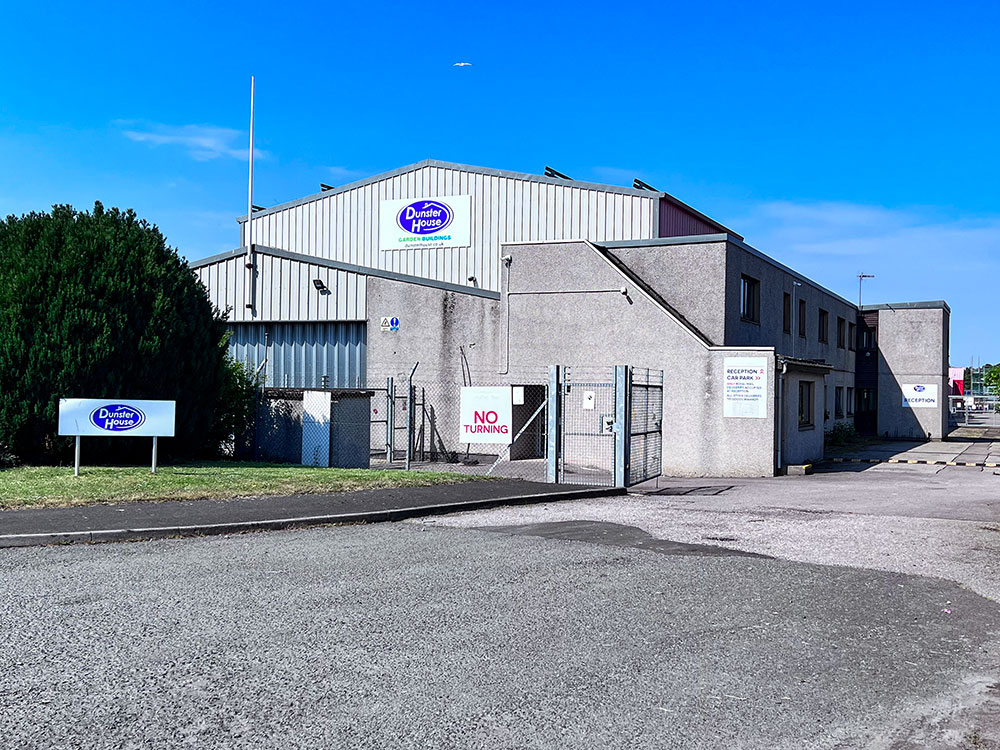
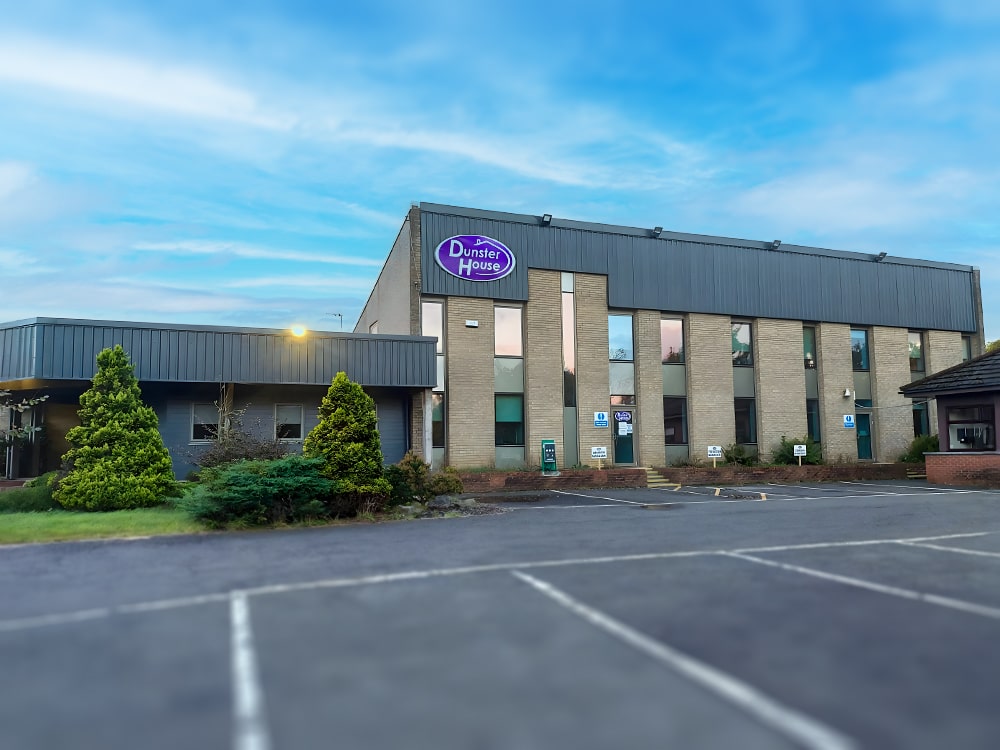


